Leider habe ich keine allzu guten Bilder von während der Arbeit. Bei Fragen, meldet euch einfach!
Diese Arbeit ist abgeleitet und inspiriert von den Demonstartionsobjekten von Epilog. Siehe dazu die Spieluhr und die Version mit Einlegearbeit. Die Spieluhr selbst wurde bei spieluhr.de bestellt. Im Prinzip lässt sich jede Spieluhr verwenden; es wären auch elektrische Modelle denkbar. Auch gibt es Modelle, die noch einen Stopper haben, der vom Deckel herunter gedrückt wird.
Als Furnier bezeichnet man dünne Holzblätter, die meist mit einem Messer vom Holzstamm abgetrennt wurden. Man verwendet sie zum Dekorieren und optischen Aufwerten von Holzarbeiten. Eine Spezialität ist die Einlegearbeit beziehungsweise die Intarsie, bei der man Furniere in die Oberfläche des Werkstückes so einbringt, dass sie eine glatte und gleichmäßige Oberfläche bilden. Dazu fräst man aus dem Werkstück eine Tasche heraus, in die man das zurechtgeschnittene Furnier dann einkleben kann.
Vorbemerkungen:
Am Besten wäre Sperrholz der Stärke 0,25 Zoll, da von diesem Material bei Epilog ausgegangen wurde. (Epilog ist ein US-Unternehmen.) Die Alternative ist entweder die Datei anzupassen (was in diesem Fall nicht trivial ist) oder sich damit „abzufinden“. Das Letztere habe ich gemacht und die überstehenden Zähne sehen eigentlich nicht schlecht aus. (Das ist natürlich Geschmackssache; muss letztendlich jeder selbst entscheiden)
Ich habe von Hand geschliffen und deswegen vor dem Schleifen das Holz ausgeschnitten. Falls ein Exzenterschleifer zum Einsatz kommt, sollte man die Anleitung von Epilog befolgen. Also erst die Furnier komplett einsetzen, dann alles plan schleifen und als letzten Schritt ausschneiden. (Ansonsten werden die Wandteile kissenförmig.) Bei dieser Methode sollte man aber darauf achten immer eine reproduzierbare Postiion auszuwählen.
Die Einstellungen des Lasers waren folgenden: Um Furnier zu schneiden habe ich ein Profil angelegt. Wichtig ist, dass es Holzfurnier ist! Auf keinen Fall darf es PVC oder ähnliches sein. Das Profil habe ich von dem für dicke Pappe abgeleitet. (Im Prinzip scheide ich mit hoher Geschwindigkeit und geringer Leistung.)
Das Gravieren von Holz muss man vorhern an einem Stück testen. Es darf nicht zu viel Material weggenommen werden, sonst verschwindet das Furnier unter der Holzoberfläche (würde das Schleifen erschweren) Es muss aber auch genügend sein, damit über die Hälfte des Furniers nach dem Schleifen noch da ist. Wenn das Furnier eingelgt ist, kann man die Kante im Optimalfall noch ganz schwach mit dem Finger spüren. Meine Einstellung war 100% Leistung, 75% Geschwindigkeit. Verwendet habe ich dafür Birkensperrholz von Modulor.
Das Schneiden hängt auch vom Holz ab und sollte ausprobiert werden. Anstatt mit hoher Leistung einmal zu schneiden, kann man auch mit geringerer Leistung und zwischenzeitlichem Senken des Fokusbereiches das Holz auf zwei Durchgängen schneiden.
Arbeitsschritte:
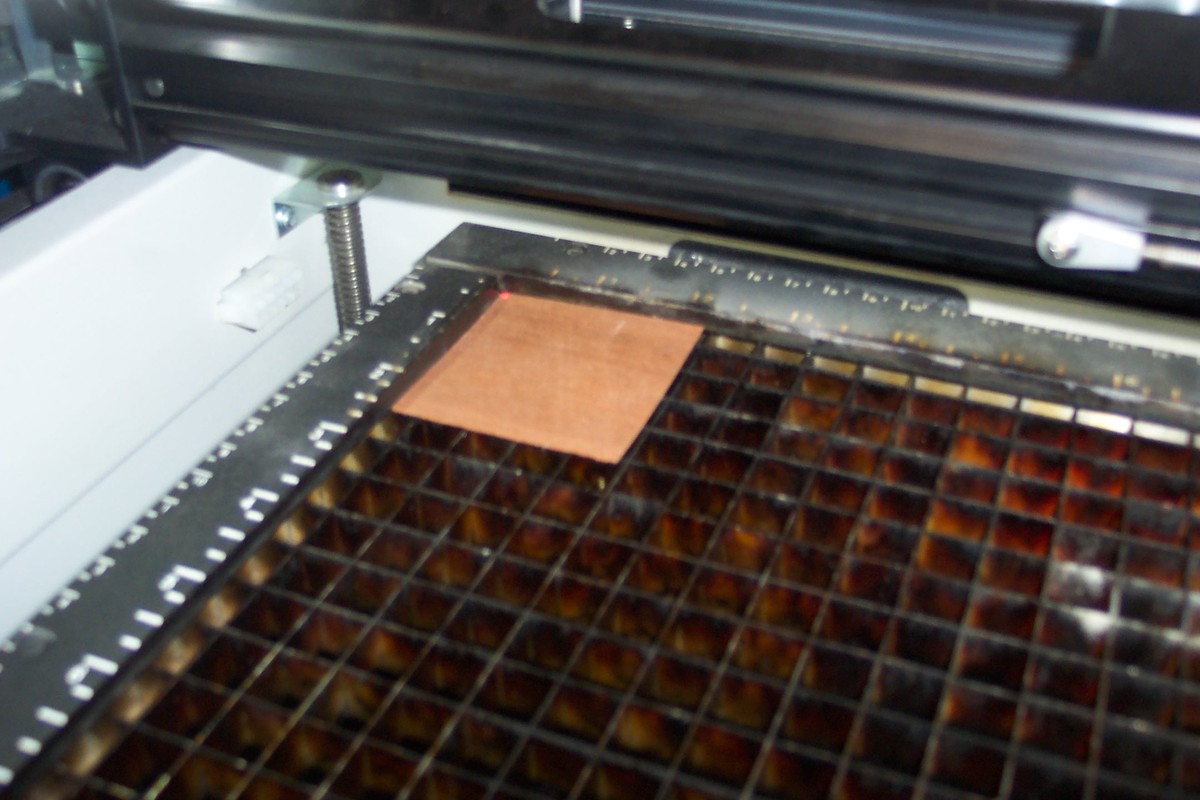
Als Erstes überlegt man sich die Farben der Furniere. Kontraste und das Spielen mit der natürlichen Maserung des Holzes kommt sehr gut heraus. Man kann sowohl heimische als auch exotische Hölzer verwenden. Exotische haben den Vorteil, dass auch ungewöhnlichere Farben verfügbar sind. Meine Furniere waren heimische, allerdings kann ich keine Bezugsquelle angeben, da ich diese aus dem Fundus meines Großvaters zog. (Wer dazu Tipps hat, möge sich bitte melden.)
Am Computer wählt man die Formen, die man mit dem aktuellen Furnier umsetzen möchte und schiebt diese platzsparend in den Ursprung. Wichtig ist dabei, dass man nur die Vektordaten schickt! Das heißt, dass die Holzblätter nicht graviert werden sollen! Eventuell dreht man die Form in der Datei, damit die Maserung auf einem Dreieck zum Beispiel immer in Richtung Spitze zeigt.
Als Nächstes verwendet man den Lasercutter, um die Taschen aus dem Holz zu „fräsen“. Falls diese tief genug sind, macht man weiter, indem man die Einzelteile ausschneidet.
Jetzt ist der Moment um die Furnierteile auf Passung zu prüfen. Dazu legt man probeweise das Furnier in die gravierten Taschen. Im Optimalfall passt die ausgeschnittenen Stücke ohne Spalt. Falls dem nicht so ist, muss entweder die Datei oder das Laserprofil angepasst werden. (Fokus prüfen; mit etwas weniger Leistung versuchen. Anders herum, falls das Furnier zu groß ist, beim nächsten Schneiden mit mehr Leistung und oder kleineren Formen in der Datei versuchen.)
Weiter geht es mit dem Einkleben der Intarsien. Dazu eignet sich Holzleim. Es empfiehlt sich ein Leim mit hoher Anfangshaftung, andernfalls muss eine Zwinge oder Furnierpresse verwendet werden. Alles- oder Sekundenkleber können auch Alternativen sein. Ein paar Teile habe ich mit Sekundenkleber geklebt und anscheinend hält es. Bei Sekundenkleber gibt man erst etwas Kleber dünn in die Tasche, haucht diesen an und wartet bis er anzieht. Dann etwas mehr Kleber hinzu geben und das Holzblättchen hineindrücken. Den Finger (der sicher kleben wird) nicht senkrecht abziehen, sondern abrollen, um das Furnier nicht abzureißen. Unabhängig davon, welcher Kleber verwendet wird, sollte der Kleber erst an einem Teststück getestet werden.
Das Endergebnis sollte ein Werkstück mit leicht überstehenden Intarsien sein. Jetzt muss das Ganze gut durchtrocknen. (Dazu die Anweisungen des Kleberherstellers befolgen)
Wenn die Klebung trocken ist, kommt das Schleifen: Zuerst mit grobem Schleifpapier solange schleifen, bis das Furnier nicht mehr übersteht, dann wird auf Papier mit mittlerer Körnung gewechselt, um etwaige Kratzer zu entfernen. Mit einem sehr feinen Papier entfernt man dann noch die Brandspuren und leichte Ungleichmäßigkeiten. Man sollte mit dem Finger keine erhabenen Stellen spüren können! Das Schleifpapier immer auf einen Holzklotz ziehen, um ein Abschrägen der Ecken zu vermeiden! (Also auch kein Schleifkissen verwenden.)
Jetzt kann man schon mal einen Vorgeschmack auf das Endergebnis sehen, indem man die Furniere ganz leicht befeuchtet.
Um die Spieluhr zu montieren diese auf die Bodenplatte auflegen und mit einem fleinem Bleistift durch die Löcher hindurch anzeichnen. Dann die Löcher für den Spanner und die zwei Schrauben bohren. Testweise sollte die Spieluhr montiert werden.
Jetzt nimmt man das Werk wieder heraus und klebt das Gehäuse zusammen. Falls hier wieder kein Leim mit hoher Anfangshaftung verwendet wird, muss für die Ecke eine Klammer verwendet werden. (Es gibt dazu Stahlklammern mit Dornen an den Enden. Diese hinterlassen jedoch kleine Spuren.)
Nach der kompletten Trocknung lackiert man das Werkstück mehrfach gleichmäßig in dünnen Schichten. Jetzt sollten die Farben der Furniere deutlich hervor treten. Herzlichen Glückwunsch, jetzt ist der Moment für einen Anflug des Stolzes gekommen 😉
Zuletzt montiert man die Spieluhr wieder. Die Schrauben sollten kräftig, aber nicht zu kräftig angezogen werden. (Die Spieluhr muss gut aufliegen und darf nicht vibrieren können. Sonst scheppert es.) Eventuell fettet man die Außenseite des Spanners mit einem Silikonfett, da diese sich beim Spielen mitdreht und dadurch etwas weniger Reibung herrscht.
Bemerkungen:
Meine Datei kann ich leider nicht veröffentlichen, da ich sie in großen Stücken aus den Daten von Epilog erstellt habe und von diesen die Rechte nicht ermitteln konnte. Falls jemand dazu etwas findet einfach melden. Aus den verfügbaren Dateien lässt sich die eigene Arbeit aber sehr einfach ableiten. In dem Fall, dass jemand hierbei Hilfe benötigt, stehe ich gerne mit Rat und Tat zur Seite. Der restliche Teil (also diese Anleitung) ist unter der genannten Lizenz veröffentlicht.